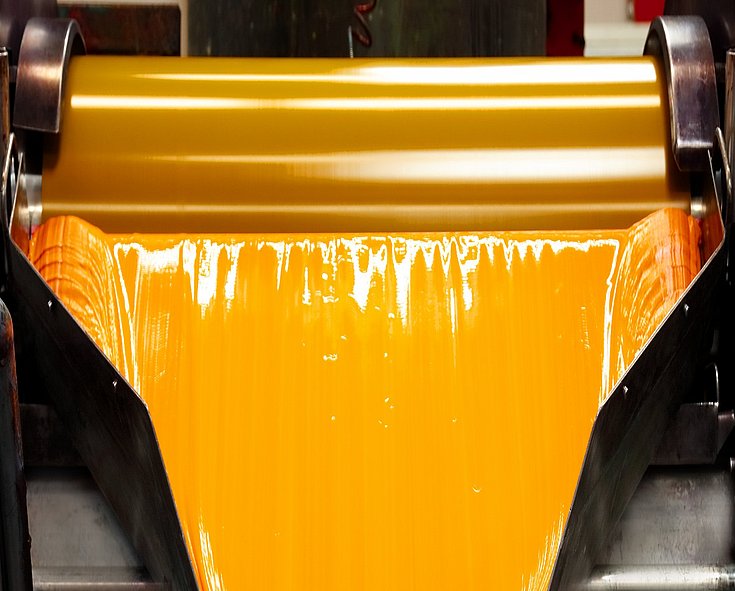
Colors are passion, emotions and personality. At Siegwerk, inks and coatings are our specialty and we use color to bring the packaging and products of our customers to life.
Siegwerk is one of the most dynamic and innovative manufacturers of UV technology for the graphic arts industry. This handbook on the theme of UV label printing provides an overview of the experience that Siegwerk has so far accumulated in this field. Our aim with this booklet is to pass on tips from practical use, possible solutions and self-help ideas. We hope that you will find it useful in overcoming any difficulties that you may encounter. The contents are divided up according to the various printing processes.
During the Corona pre-treatment, an electric charge is generated over the synthetic film substrate by means of conductors carrying a high voltage. This changes the surface tension of the film. Details
of the ideal surface tension for good ink/varnish adhesion can be obtained from your film suppliers; it is quoted in mNm (= millinewtonmeter). In the case of polyolefines (PE, PP) a surface tension of at least 39 – 45 mNm is recommended. Testing the surface tension of a film is carried out with the aid of a graduated series of test inks.
This testing is used to check the adhesion of UV inks and UV varnishes to the print substrate. Cut off a length of adhesive tape measuring approximately 10 cm in length. Place the adhesive tape slowly on the printed surface and press down with the fingers, ensuring that no air bubbles are trapped between the adhesive tape and carrier material. Pull off one end of the tape as far as the middle with a short, sharp tug, then the remainder with further short, sharp tug. Examine the adhesive tape and the print and assess the adhesion.
A more severe form of the adhesive tape test is the cross-cut adhesion test. Here the kiss cutting, and therefore the 'injury' to the ink/ varnish film is simulated. The ink film is scored crossways, and then the adhesive tape test is carried out on the ink film, which has been damaged in this way. Suitable cross-cut adhesion test apparatus is available from suppliers of graphic arts laboratory equipment.
There are no standards for this simple test, and it calls for a degree of experience on the part of the printer. It is carried out by drawing a fingernail over the printed surface, using light pressure. If the surface is damaged, it indicates inadequate curing or an excessively soft ink film. In this case the addition of wax or abrasion protection pastes - or varnishing over the print in the case of high demands - is recommended.
This test makes use of the fact that an aqueous solution of potassium permanganate (KMnO4) will oxidize any unreacted acrylate components in UV varnish, causing them to darken in color. The optical density of the surface spots caused by the solution is measured using a densitometer. The darker the spot, the poorer the drying and the slower the curing of the varnish film is said to be. The result of the measurement is compared to a measurement carried out on a well-cured UV varnish of the same type. Comparisons between two different varnishes are meaningless. Using a pipette, apply a drop of a 5% aqueous solution of KMnO4 onto the varnished area directly after printing and curing. Allow the solution to react for 5 minutes. Dab off the excess solution with absorbent paper (do not wipe). Measure the optical density of the spot and record the figure.
In view of the large number of product durability requirements, the variety of different test methods and the widely varying substances used, it is impossible in such a guide to give a general recommendation with respect to the specific UV inks and varnishes that are to be used.
Please check the exact requirements, test conditions and substances before carrying out a production run. Our application technicians will be pleased to offer you their assistance and help you to find a solution to any problem.
Combination printing has developed to become a totally routine process in modern label production and it has become an indispensable part of this industry. Nevertheless, the combination of different printing processes poses stiff challenges for the printing ink systems employed.
Due to the different viscosities and surface tensions of the ink systems being used together in combination, problems may be encountered with the flow or lay down of the ink during overprinting.
A major step forward in solving this problem was made in the development of silicone-free ink systems.
However, since even very small quantities of incompatible flow additives (such as silicone for example) may lead to imprintability problems, it is of paramount importance to adhere to the following parameters before using silicone-free inks for the first time:
Fit clean new screens.
Clean the anilox rollers and storage containers thoroughly during any changeover.
Use only washing agents and cleaning cloths that have not come into contact with other ink systems or silicones.
Thorough cleaning of the machine, pumps and hoses, and in the case of UV screen printing and flexo printing, the doctor blade system.
During daily production of labels with UV-inks and varnishes, some problem can occur regardless of the applied printing method. On the following pages, we would like to show solutions in order to solve these problems easily and efficiently.
Excess inking, especially with dark colors, opaque white or metallic inks.
Untreated print substrates:
Bad intercoat adhesion: the ink is over-hardened.
Reduce layer thickness, if necessary by the choice of a suitable printing process in combination printing
Poor quality embossing, muddy printing:
Protection pastes or lubricants may not be used.
Ink is over-cured:
are essential, as is the right hot stamping temperature and use of suitable hot stamping foils.
Over-hardening (ink flaking at the cutting point), mainly with light colors:
In the case of poor die-cutting performance of UV-screen opaque white:
Please contact the application engineers at Siegwerk about appropriate UV ink types. We will be pleased to help you and provide you with support in solving your problems.
Check the settings of the ink rollers to the oscillating roller. Check the settings (pressure) of the rollers to the printing plate.
Gear marks are most often caused by mechanical problem of the printing press. Please contact your press manufacturer.
This phenomenon appears most currently if the substrate used is highly stressed due to temperature changes. If the printed substrate is stretched and then shrunk again, the dried ink film cracks. This problem appears as well in card printing, when that cards are laminated under heat and pressure.
If feasible use substrates with a higher temperature resistance, you may possibly use special inks that are more resistant.
When using fanal inks, the print can bleed if it comes in contact with solvent based products or even UV-laminating adhesives containing amines.
The light fastness of a printing ink depends mostly from the pigment used in the formulation. This resistance is indicated according to the wool scale (WS) and is in between 1 (worst) and 8 (best).
Set-off or migration of waxes or silicone-acrylates can influence the reaction of the thermal coating negatively.
The darkening during the thermal printing can therefore not be guaranteed anymore.
Area of application: solid areas, half-tone and line work. Ink usage: approx. 6–20 g/m2.
Excess inking, especially with dark colors, opaque white or metallic inks. Screen printing inks are intended to be applied at a thickness of approx. 6 – 15 μm. Thick applications may lead to adhesion problems.
Bad intercoat adhesion: the ink is over-hardened.
Reduce the output of the UV lamp.
Do not add flow agent to the ink which is printed first.
Use thinner to optimize the flow.
For example for fine typefaces. If the ink is too thin, add 10% Thixpaste.
Area of application: solid areas and half-tone work. Ink usage: approx. 1.5 – 6 g/m2.
The ink thickness is governed by the choice of anilox roller. Here approx. 35% of the theoretical volume drawn is actually transferred to the print substrate.
The use of the anilox roller must therefore be matched to the print subject.
As a result of incompatible surface tensions between different ink systems, UV flexo inks may cause flow problems on the pre-printed UV screen printing opaque white.
The printing may take on a ‚"cloudy" appearance according to the nature of the surface and absorbency of the print substrate.
Area of application: half-tone and linework Ink usage: approx. 1.2–1.6 g/m2.
The layers of a blanket are almost identical to the construction
of the elastomer rollers. Swelling of the blanket can result in an increase in pressure and thus lead to inconsistent ink transfer between plate/blanket and blanket/print substrate with a direct effect on printing quality. It is therefore necessary to use appropriate blankets when using UV inks. Please contact your blanket supplier about this.
The photopolymer coating on positive plates is not always resistant to UV cleaning agents. If this type of plate is being used, the coating must be baked in accordance with the manufacturer’s instructions. A positive plate treated in this way is resistant to the majority of UV cleaning agents. When using negative plates, baking is not generally necessary.
Ink supply too high.
In the offset process due to emulgated dampening solution.
In waterless UV offset printing due to separation of the printing ink at low press temperature (Silicone is separating from the printing ink).
Back-splitting of the printing ink from the substrate to the blanket. Therefore heavy ink build-up on the blanket. Depending on the surface tension and on the surface smoothness of the substrate.
Tack of the printing ink is too high:
Due to migration of softeners or antistatic agents to the surface of the substrate (especially with soft PVC) a uniform print is made impossible.
The way to check if this is the case, is to clean the surface of the substrate with alcohol and to make a short print trial with the cleaned samples. These samples shall then show a uniform print again.
Substrate exhibits bad picking resistance.
Reduce the quantity of fountain solution being applied to the plate.
Viscosity and tack of the ink too low.
In UV offset, dot gain is slightly greater than with conventional offset. This is dependent, among other things, on the vehicle system being used and may vary from one ink system to another.
Adjustment of the printing reference line should compensate for the more pronounced dot gain.
Area of application: Half-tone and linework, ink usage: approx. 1.8–2.2 g/m2.
If the ink is too soft, drying problems may be experienced on account of the greater layer thickness at the edge of the printed area. As a rule, this leads to drying problems, particularly in the case of dark and/or metallic inks.
If negative typefaces clog up, add 5 – 10 % Thixpaste.
Substrate exhibits bad picking resistance.
Ink supply too high.