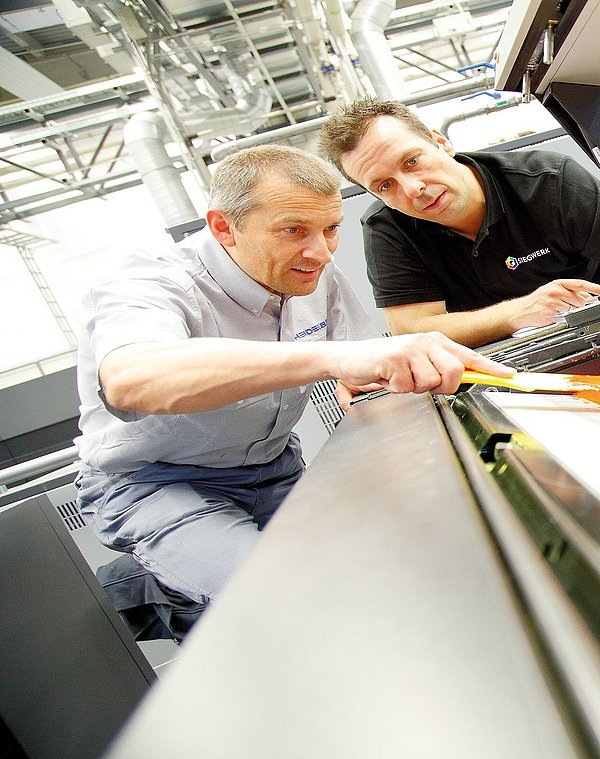
Etikettendruck Ratgeber
Hier erhalten Sie sofortige Lösungen rund um das Thema Sicura UV Farben.
Der Siegwerk Ratgeber für den Etikettendruck bietet Ihnen die Möglichkeit, Probleme schnell zu erkennen und zu beheben und so die Produktivität im Druck zu steigern.
Allgemeine Fragen rund um UV-Etikettendruck
Ton, Farbintensität und Transparenz einer Druckfarbe hängen vor allem von den Eigenschaften der verwendeten Pigmente ab. Für UV-Farben werden hauptsächlich organische Pigmente eingesetzt, viele davon werden auch für andere Druckverfahren verwendet, so dass UV-Farben im Regelfall die gleichen farbmetrischen Eigenschaften wie diese aufweisen.
Auf speziellen Wunsch und nach Laborabklärungen sind auch reine Farbtöne (z.B. Fanalfarben) lieferbar. Dazu müssen jedoch der Original-Bedruckstoff und die genauen Spezifikationen (Druckverfahren, Verwendungszweck) mitgeteilt werden.
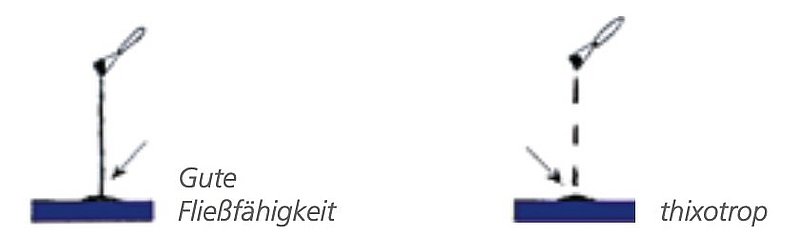
Viskosität und Fließfähigkeit beeinflussen das Nachfließen und den Transport der Farben im Farbkasten und im Walzenstuhl und damit die Farbverteilung in der Maschine. UV-Farben sind je nach eingesetztem Pigment meist kompakter und schlechter nachfließend als konventionelle Druckfarben. Empfehlenswert ist der Einsatz von Rührwerken im Farbkasten, um die optimale Farbverteilung zu gewährleisten.
Anders als bei konventionellen Druckfarben oder Flüssigfarben auf Wasser- oder Lösemittelbasis müssen bei UV-Farben keine Lösungs-mittel/Verdünner durch Verdampfen oder Absorption entfernt werden. Alle reaktiven Bestandteile sind am Polymerisationsprozess, also der Härtung des Farb-/Lackfilms, beteiligt. Die beim Druck-prozess übertragene Farb-/Lackmenge bleibt zu 100% auf dem Bedruckstoff erhalten. Dadurch ist die UV-Technologie aus der Sicht des Umweltschutzes eine der saubersten Technologien.
Wegen ihrer hohen Polaritäts- und Löslichkeitswerte können UV- Bindemittel das Aufquellen oder Schrumpfen bestimmter Elastomere verursachen, aus denen herkömmliche Walzen und Gummidrucktücher bestehen. Materialien wie Polyurethan sollte man deshalb durch UV-kompatible Materialien wie Butyloder Nitrilgummi ersetzen. Diese Stoffe quellen nur minimal auf und sind trotzdem auch mit konventionellen Druckfarben auf dem gleichen Walzenstuhl verwendbar. Werden auf der Maschine ausschließlich UV-Farben und UV-Lacke eingesetzt, sollte man Farbwalzen
aus UV-resistentem EPDM-Kunststoff verwenden.
Bestandteile in UV-Produkten, wie Acrylate, Monomere und Fotoinitiatoren, können bei wiederholtem direktem Hautkontakt bei empfindlichen Menschen zu Reizungen, Allergien oder Hypersen-sibilisierung führen. Das Informationsblatt der EUPIA „Guidelines for the Safe Use of Energy Curing Printing Technology”, die Sicherheitsdatenblätter und Informationsblätter lokaler Berufsorganisationen enthalten präzise Angaben über die Gefahr von Reizungen und Allergien sowie grundsätzliche Richtlinien für den Umgangmit UV-Farben und -Lacken.
Anwendungsgebiet: Flächen und Rasterarbeiten.
Farbverbrauch: ca. 1,5– 6 g/m².
Die Farbstärke wird durch die Wahl der Rasterwalze beeinflusst.Dabei wird ca. 35% des theoretischen Schöpfvolumens effektiv auf den Bedruckstoff übertragen. Der Einsatz der Rasterwalze muss daher auf das Drucksujet abgestimmt sein.
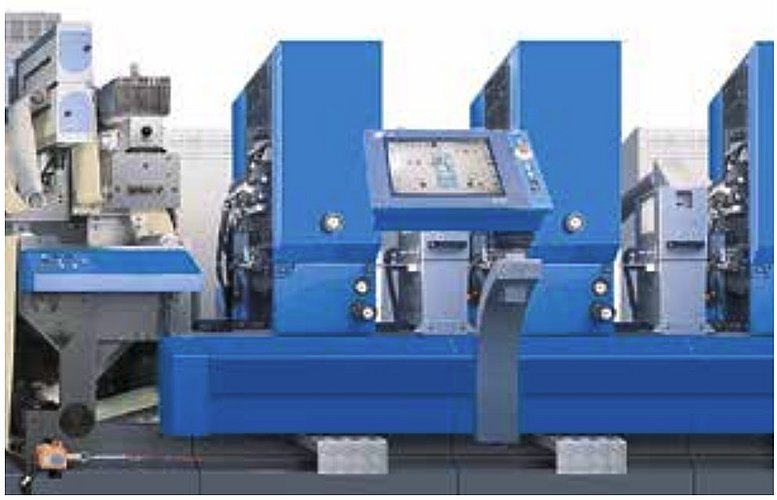
Anwendungsgebiet: Raster- und Stricharbeiten.
Farbverbrauch: ca. 1,2–1,6 g/m².
Anwendungsgebiet: Flächen, Raster- und Strich-Arbeiten.
Farbverbrauch: ca. 6–20 g/m².
Fragen rund um die Prüfung von UV-Etikettendruck
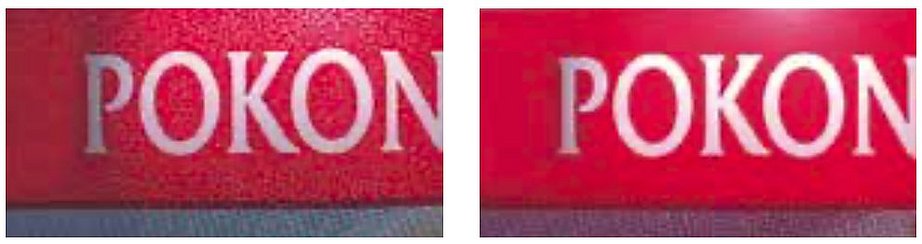
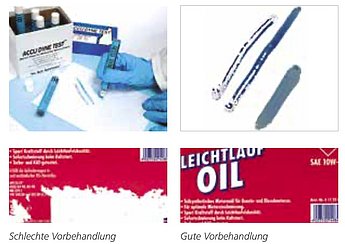
Bei der Corona-Vorbehandlung wird über der zu bedruckenden Folie mittels hochspannungsführendem Leiter eine elektrische Entladung erzeugt, welche die Oberflächenspannung der Folie verändert. Die ideale Oberflächenspannung für gute Farb-/Lackhaftung erfragen Sie am besten bei Ihrem Folienlieferanten; sie wird in mNm (= Milli-Newtonmeter) angegeben. Bei Polyolefinen (PE, PP) ist eine Oberflächenspannung von mindestens 39 – 45 mNm erforderlich. Die Prüfung der Oberflächenspannung wird mit einer Reihe abgestufter Test-Tinten durchgeführt.
Bei der Prüfung von Trocknung von UV-Lacken macht man sich zunutze, dass Kaliumpermanganat (KMnO4) in wässriger Lösung mit den nicht reagierten Acrylatbestandteilen im UV-Lack oxydiert und diese dunkel verfärbt (Braunsteinbildung). Die optische Dichte der von der Lösung auf der Oberfläche verursachten Flecken wird mit dem Densitometer gemessen. Je dunkler der Fleck, desto schlechter die Trocknung bzw. langsamer die Härtung des Lackfilms. Vergleiche zwischen unterschiedlichen UV-Lacktypen haben nur bedingten Aussagewert.
Mit einer Pipette einen Tropfen einer 5%-igen KMnO4-Lösung direkt nach Druck und Härtung auf die lackierten Bereiche auftragen. Die Lösung 5 Minuten lang einwirken lassen. Die überschüssige Lösung mit einem saugfähigen Papier abtupfen (nicht wischen). Danach die optische Dichte des Flecks messen und den Wert aufzeichnen.
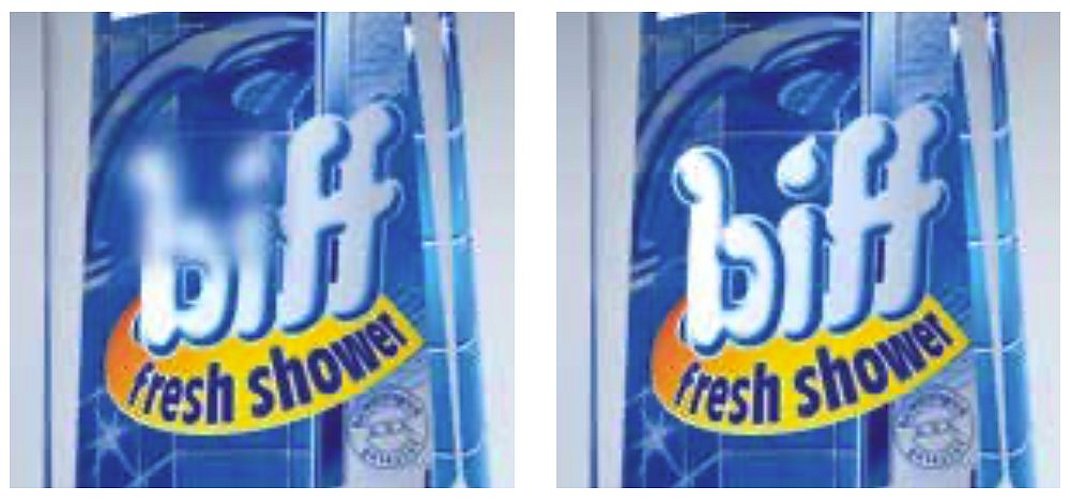
Aufgrund der Vielzahl geforderter Produktbeständigkeiten, der verschiedenen Testmethoden und unterschiedlichster Substanzen,die zum Einsatz gelangen, kann keine generelle Empfehlung für einzusetzende UV-Farben und -Lacke gegeben werden. Bitte klären Sie im Vorfeld einer Produktionsauflage die genauen Anforderungen, Testbedingungen und Substanzen ab. Unsere Anwendungstechniker sind Ihnen dabei gerne behilflich und unterstützen Sie bei der Problemlösung.

Mit dieser Prüfung wird die Haftung von UV-Farben und UV-Lacken auf dem Bedruckstoff kontrolliert. Ein etwa 10 cm langes Stück Klebband zuschneiden. Das Klebband langsam auf die Druckfläche auflegen und mit dem Finger andrücken, sodass keine Luftblasen zwischen Klebband und Trägermaterial eingeschlossen sind. Dann das Klebband mit einem kurzen, scharfen Ruck bis zur Mitte abziehen, dann den Rest mit einem weiteren kurzen Ruck wegreißen. Das Klebband und den Druck untersuchen und die Haftung bewerten.
Eine verschärfte Form des Klebbandtests ist der Gitterschnitttest. Dabei wird das Anstanzen und damit das ‚Verletzen’ des Farb-/Lackfilms simuliert. Der Farbfilm wird kreuzweise eingeritzt, und der Klebbandtest wird auf dem so verletzten Farbfilm durchgeführt. Entsprechende Gitterschnitttestgeräte sind in Geschäften für grafischen Laborbedarf erhältlich.
Diese einfache Prüfung ist nicht genormt und bedingt eine gewisse Erfahrung des Druckers. Dabei wird ein Fingernagel mit leichtem Druck über die Druckoberfläche geführt. Wird diese beschädigt, zeigt dies eine mangelhafte Durchtrocknung oder einen zu weichen Farb-film an. In diesem Fall wird das Zumischen von Wachs- oder Scheuerschutzpasten oder bei hohen Ansprüchen das Überlackieren des Drucks empfohlen.
Fragen und Antworten rund um UV-spezifische Druckprobleme
Je nach Oberflächenbeschaffenheit und Saugfähigkeit des Bedruckstoffes kann der Druck ‚wolkig’ aussehen.
- Wenn möglich, die Mischfarbe mit Deckweiß anstatt mit Verschnitt/Transparentweiß ausmischen.
- Vordrucken eines Transparentweiß bzw. Firnis, um die ‚Poren’ saugfähiger Substrate zu schließen.
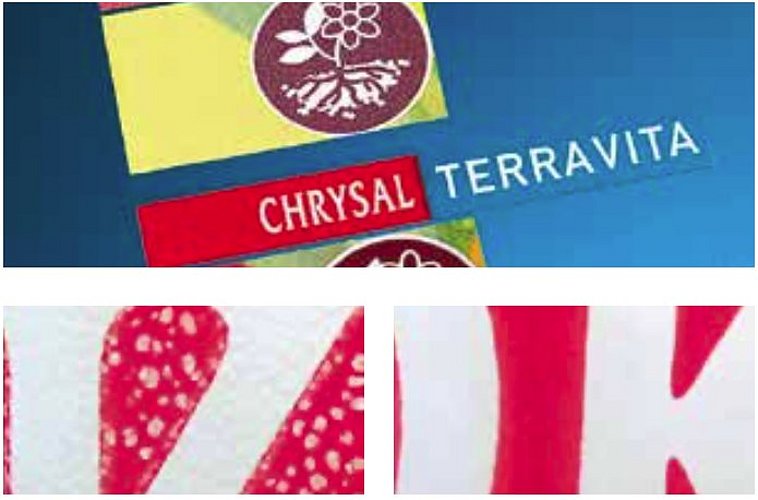
Aufgrund nicht abgestimmter Oberflächenspannung unterschiedlicher Farbsysteme können UV-Flexofarben auf dem vorgedruckten UV-Siebdruck-Deckweiß Verlaufsstörungen verursachen.
- Geeignetes, wenn möglich, additivfreies Siebdruckweiß vordrucken.
- Verlauf der Flexofarben mit geeigneten Additiven einstellen, die mit denen des Siebdruckweiß abgestimmt sind.
- Wenn möglich, die Verlaufsstrecke zwischen Druckwerk und UV-Strahler verlängern.
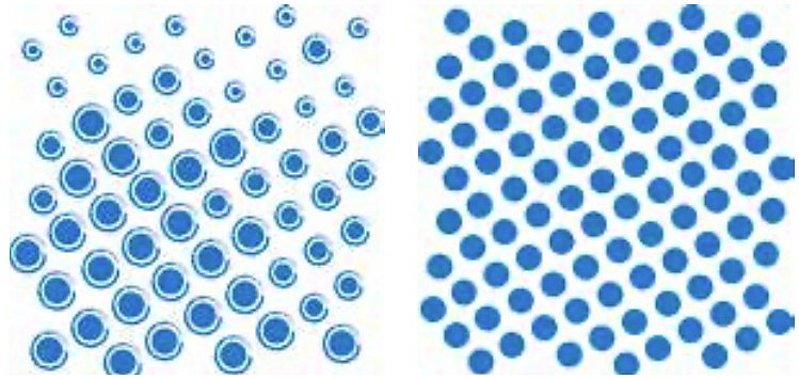
Beim Einsatz zu weicher UV-Farbe oder bei einer Überfärbung des Druckbildes kann es zu einer Bildung von
Quetschrändern kommen. Dies führt im Regelfall zu Trocknungsproblemen, besonders bei dunklen und/oder Metallicfarben.
- Die Farbe wenn möglich unverschnitten ohne Additive einsetzen.
- Gegebenenfalls höher konzentrierte Farbe einsetzen.
Wenn Negativschriften zusetzen, 5–10 % Thixpaste zugeben.
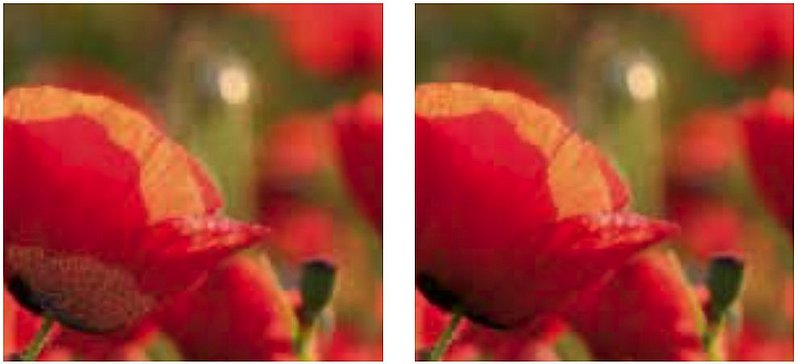
Schlechte Rupffestigkeit des Bedruckstoffs.
- Herabsetzen des Tacks der eingesetzten Farbe durch Beimischen von Anti-Tack-Paste.
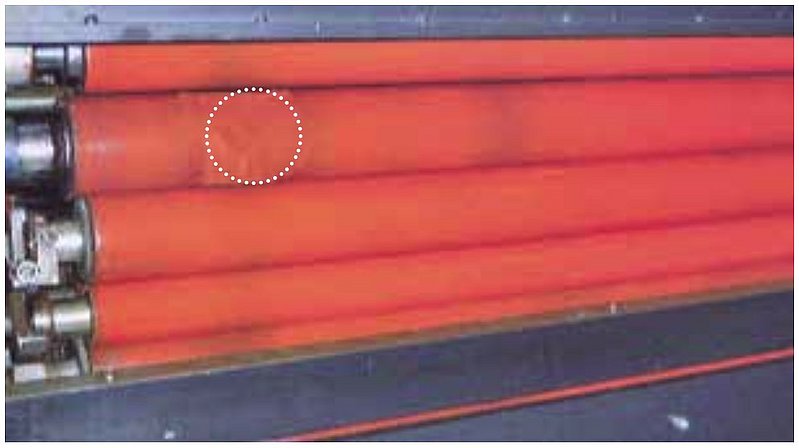
Zu hohe Farbführung.
- Die Farbmenge reduzieren oder konzentriertere Farbsystemeverwenden
- Einstellung der Farbwalzen überprüfen
- Ungeeignetes Walzenmaterial auswechseln
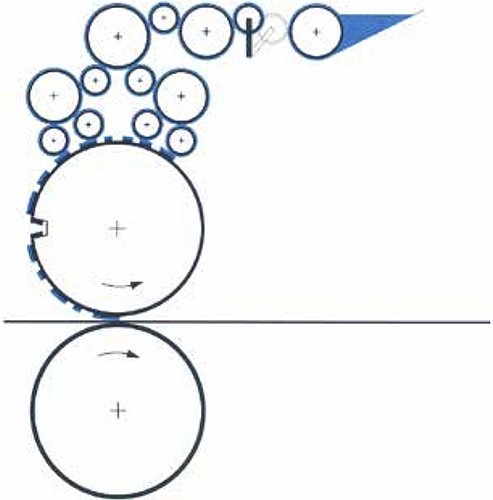
Anwendungsgebiet: Raster- und Stricharbeiten, Farbverbrauch:ca. 1,8–2,2 g/m².
Schlechte Rupffestigkeit des Bedruckstoffs.
- Möglicherweise ist die Zügigkeit des Gummituchs zu hoch;
- Qualität des Gummituchs überprüfen.
- Herabsetzen des Tacks der eingesetzten Farbe durch Beimischen von Anti-Tack-Paste.
Zu niedrige Viskosität und Tack der Farbe.
- Farb-Wasser-Balance überprüfen.
- pH-Wert des Feuchtwassers überprüfen.
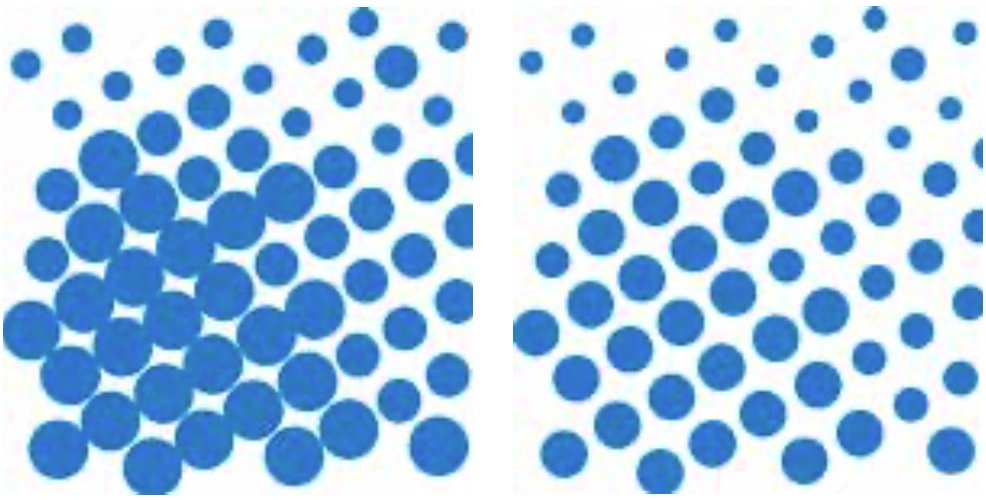
Im UV-Offset ist die Punktzunahme geringfügig stärker als im konventionellen Offset.
Dies ist u.a. abhängig vom eingesetzten Bindemittel und kann von Farbsystem zu Farbsystem variieren.
Durch Anpassung der Druckkennlinie sollte man der stärkeren Punktzunahme Rechnung tragen.
- Einstellung der Farbwalzen überprüfen.
- Druckbeistellung überprüfen.
- Dicke des Gummituchaufzugs überprüfen.
- Härtere Walzen oder Gummitücher einsetzen.
Zu hohe Feuchtwassermenge reduzieren.
- Druckbeistellung überprüfen.
- Zu hartes Gummituch auswechseln.
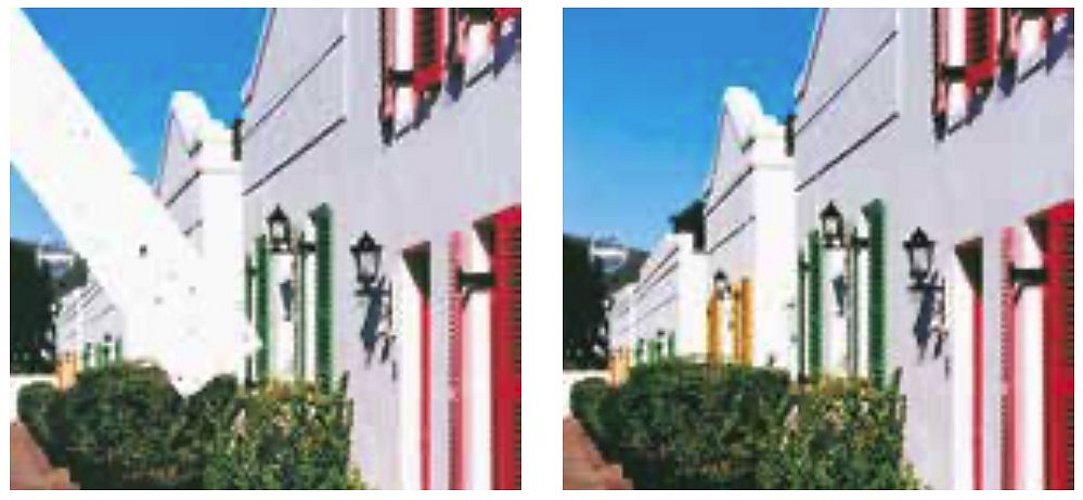
Zu starker Farbauftrag, speziell bei dunklen Farben, Deckweiß oder Metallic-Farben. Siebdruckfarben sind für eine Schichtdicke von ca. 6 –15 μm vorgesehen. Bei hohen Schichtstärken können Haftungsprobleme entstehen.
- Wenn möglich, feineres Sieb verwenden.
- Verschnittlack beimischen.
- Fotoinitiatoren beimischen.
Beim Übereinanderdruck: Die Farbe ist zu stark ausgehärtet.
- Strahlerleistung reduzieren.
- Der vorausgededruckten Farbe kein Verlaufmittel zugeben.
Den Verlauf mittels Verdünner optimieren.
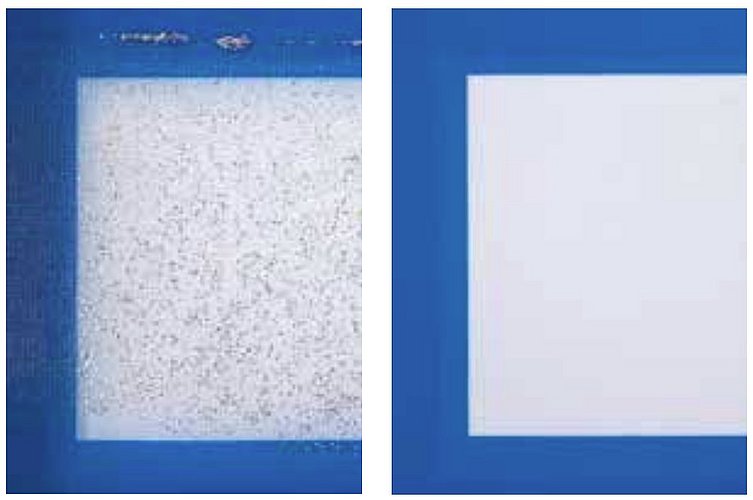
- Siebe vor Sonnenlicht und anderen Lichtquellen schützen.
- Bei Einsatz von Farben und Lacken mit Härter oder Haftvermittler das Sieb sofort nach dem Druck oder bei Maschinenstillstand reinigen.
- Bei Metallic-, Perlglanz- und Effektfarben muss die Maschenweite des Siebes so gewählt werden, dass sie das 2,5-fache der Pigmentgröße beträgt.
- Mischtöne, wenn möglich, mit einem Anteil Deckweiß ausmischen (bis 10 %).
- In vorsichtigen Schritten von ca. 1 % bis max. 15 % Verdünner zugeben, bis das gewünschte Resultat erreicht ist.
- Die Kombination von 2 % Verlaufmittel und 5 % Verdünner zeigt meistens gute Erfolge, ist jedoch abhängig von Bedruckstoff, Oberflächenspannung, Druckmaschine und der Druckgeschwindigkeit.
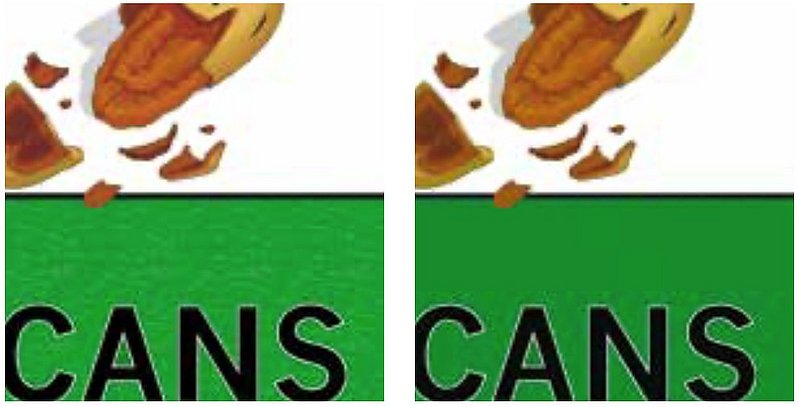
Zum Beispiel bei feinen Schriften. Falls die Farbe zu dünn ist: Zugabe von 10% Thixpaste.
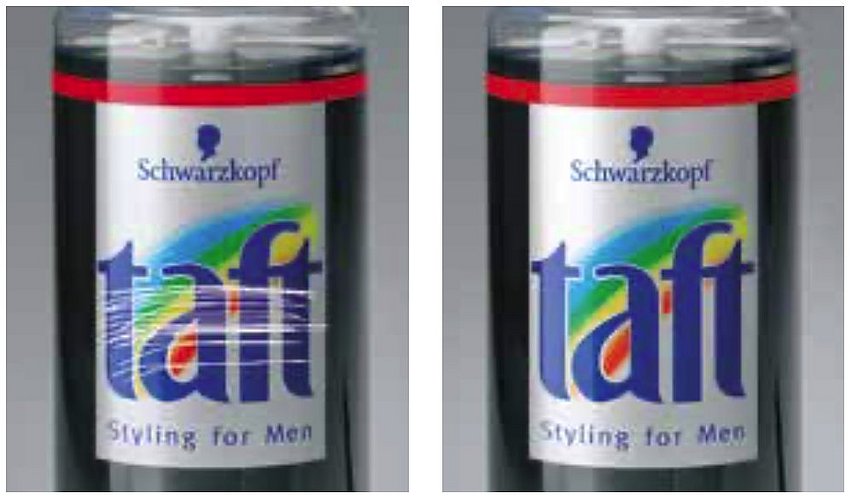
Schichtstärke verringern, gegebenenfalls durch Wahl eines geeigneten Druckverfahrens im Kombinationsdruck
- Dunkle Farbtöne wenn möglich am Anfang drucken.
- Im Sieb- oder Flexodruck reduzieren der Farbschicht durch Verwendung feinerer Rasterwalzen respektive Siebe.
- Bei Aufträgen, die nicht lackiert werden, sollten der letzten Farbe 3–5% Scheuerschutzpaste beigefügt werden, um die mechanischen Beständigkeiten des Drucks zu verbessern.
Unsaubere Prägung, unsauberer Druck:
- Geeignete, möglichst additivfreie Farbsysteme einsetzen.
- Wachs- oder silikonhaltige Additive, wie Verlaufsmittel, Scheuerschutzpasten oder Gleitmittel, dürfen nicht zugemischt werden.
Farbe ist zu stark ausgehärtet:
- Druckreihenfolge ändern oder die Strahlerleistung verringern. Korrekte Einstellung der Thermotransfer- bzw. Prägewerkzeuge sind Voraussetzung, ebenso die richtige Prägetemperatur und der Einsatz der geeigneten Prägefolien.
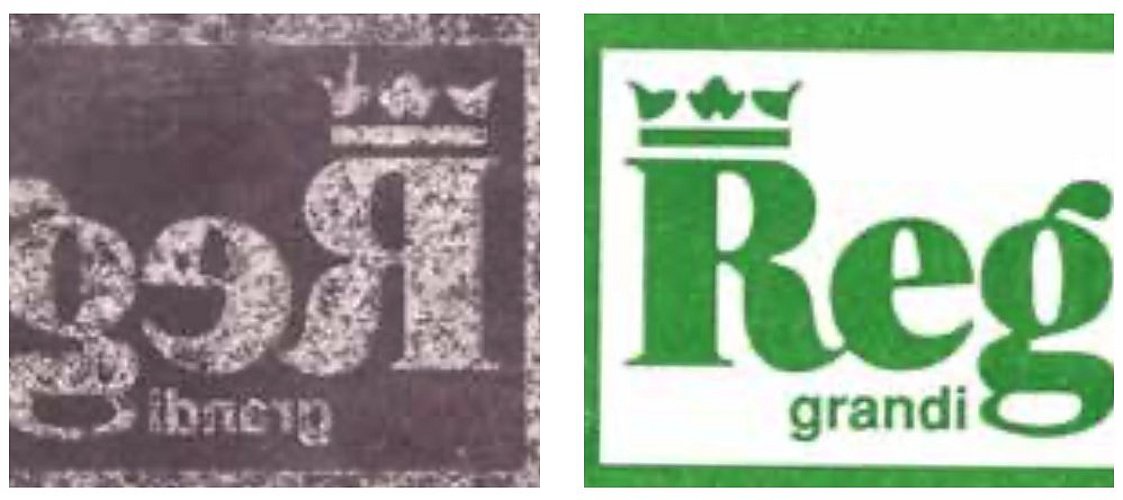
Abklatsch oder Migration von Wachsen oder Silikonacrylatenkönnen die Reaktion der Thermoschicht
negativ beeinflussen. Eine Reaktion bzw. Schwärzung der Thermoschicht (Eisenstearat oder Lactone) ist somit nicht mehr gewährleistet.
- Verwendung von geeigneten additivfreien Farbsystemen.
- Eventuell Wickeldruck reduzieren.
Zu starke Aushärtung (absplitternde Farbe an Stanzstelle), vor allem bei hellen Farbtönen:
- Druckreihenfolge ändern oder die Strahlerleistung vermindern.
Bei schlechter Stanzfähigkeit des UV-Siebdruck-Deckweiß:
- Weicheres Deckweiß verwenden.
- Stanzwerkzeug überprüfen.
Wegen geeigneten UV-Farbtypen sprechen Sie die Anwendungstechniker von Siegwerk an. Wir sind Ihnen gerne behilflich und unterstützen Sie bei der Problemlösung.
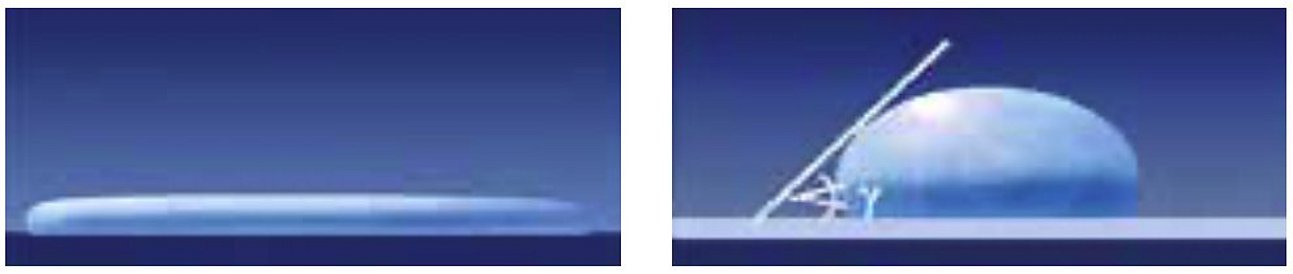
Der Kombinationsdruck hat sich in der modernen Etikettenproduktion zu etwas absolut Alltäglichem entwickelt und ist heute in dieser Industrie nicht mehr wegzudenken. Trotzdem stellt die Kombination der verschiedenen Druckverfahren sehr hohe Anforderungen an die eingesetzten Druckfarbensysteme.
Bedingt durch unterschiedliche Viskositäten und Oberflächenspannungen der miteinander kombinierten Farbsysteme können Störungen beim Verlauf oder dem Liegen der Farbe im Übereinanderdruck entstehen. Mit dem Einsatz silikonfreier Farbsysteme wurde ein großer Beitrag zur Lösung dieser Problematik geleistet.
Da aber bereits kleinste Mengen von nicht aufeinander abgestimmten Verlaufsadditiven (u.a. Silikone) zu Verlaufsstörungen führen können, ist es von größter Wichtigkeit, vor dem ersten Einsatz silikonfreier Farbsysteme folgende Parameter einzuhalten:
- Neue, saubere Siebe einsetzen.
- Rasterwalzen und Vorratsbehälter bei Umstellung gründlich reinigen.
- Nur Waschmittel und Reinigungstücher benutzen, die nicht in Kontakt mit anderen Farbsystemen oder Silikonen gekommen sind.
- Gründliche Reinigung der Maschine, besonders der Pumpen und der Schläuche.