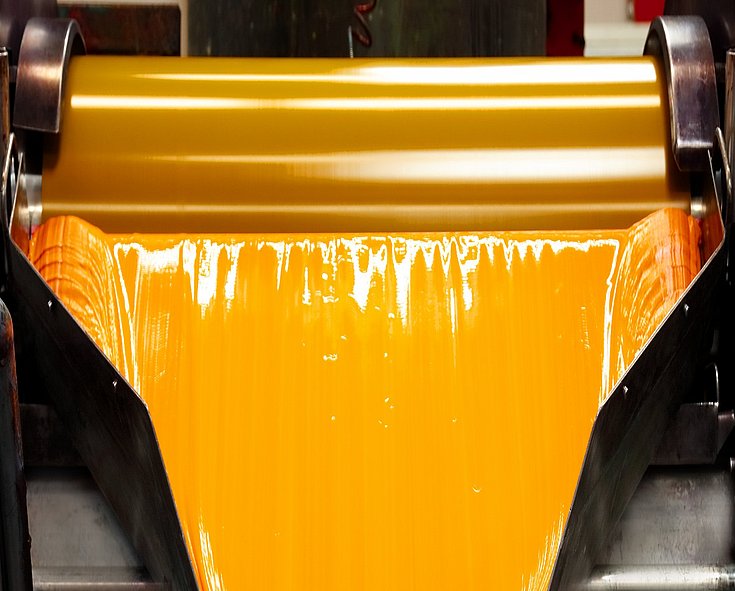
Colors are passion, emotions and personality. At Siegwerk, inks and coatings are our specialty and we use color to bring the packaging and products of our customers to life.
A performance test at laboratory (Siegwerk Vietnam). The high-resolution camera allows to capture the fingerprint images in detail that supports the expert on his assessment.
The adopted solution uses a head-mounted device “RealWear HMT-1Z1,” which is designed to be deployed in noisy industrial environments. The device connects via a software application that allows Siegwerk experts to interact with customer or in-house technicians remotely. HMT-1Z1 is equipped with a high-resolution camera and Assisted Reality (aR) technology platform. It provides the users with an immediate field of vision and removes overlaid information with a real-world view. In other words, the expert is capable of seeing whatever the technician is looking at. An integrated speaker and double microphones are available on the device for hands-free voice control and conversation.
Inkconnect is therefore an effective and practical solution in these social distancing times. If a problem occurs, the customer or in-house technician can call the experts and show them a detailed screen view in a few minutes thanks to RSS. Then he or she can receive immediate instructions from the experts while handling the issue with both hands free. For complicated problems, an online group meeting can be opened up to involve other experts for further discussions.
What are the benefits?
• Increase safety thanks to hands-free solutions
• Enable technicians to remotely collaborate with offsite experts in real time
• Cost savings, reduced waiting time, and machine downtime
• Increase productivity and efficiency – experts can provide immediate assistance while hands-free communication allows technicians to use both hands for troubleshooting
• Reduce operational costs – greatly increase first-time fix rates or speed up completion of testing evaluation
The PMC team has completed some experiments at the Vietnam site so far. It tested the device connectivity, voice recognition and camera quality in a laboratory as well as warehouse environment. Besides hardware, software application was also carried out for the trials of features such as taking photos, videos, live drawings, notes and group meetings. Some minor adjustments will be needed, for example the improvement of streaming quality, but all the tests showed promising results and advantages. “Direct visual technical support shared with the experts allows for advising points of action immediately. This will save customer downtime and waste and speed up approval processes”, Dean commented. “We must realize that this assisted support apparatus will need strong IT local support, meaning good connection for this system to perform well.” This solution is currently offered to support the customer during the restricted travelling period and to get more practical user experience. Moving forward, we are planning to use the HMT-1Z1 for troubleshooting with immediate support at press, machine/equipment installation, quality improvement meetings and online training (practical observation).