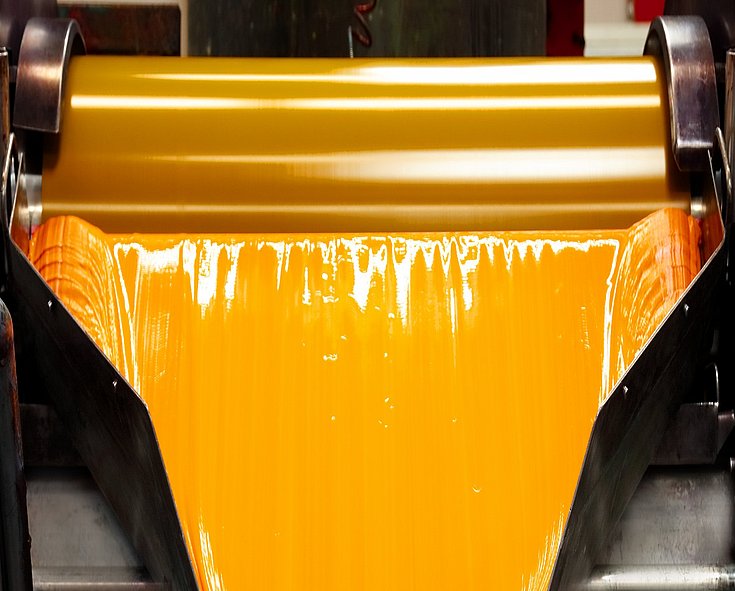
Colors are passion, emotions and personality. At Siegwerk, inks and coatings are our specialty and we use color to bring the packaging and products of our customers to life.
Moving from a manual system, MyInkRoom was a logical choice for inventory and order processing needs of our young company. It was easy to learn, intuitive to use and provided a platform to streamline our order processes. Chai Min Piau, Executive Director, Hexachase Flexible Packaging Sdn Bhd
Managing ink stock and inventory is an ongoing challenge for many printers today – especially due to numerous manual processes. It often is very time-consuming and can easily lead to mistakes. To keep the correct balance between high and low consumed inks is anything but easy.
Discovering this pain point of its customers, Siegwerk has developed a digital platform called MyInkRoom to exactly manage the balancing act between low inventory and high production planning flexibility. It is a vendor management application which can be tailored to customer’s specific needs. The app provides automated functions helping customers to reduce manual process steps including stock counting and paper works by providing a fast, simple real-time overview of the entire inventories and dosing ranges as well as other custom KPIs at any time (24/7). It offers the opportunity to define product-specific reserve inventories or have them automatically computed. If stocks fall below a minimum level, the system can also prepare automated orders for replenishment in time. All in all, the digital platform can add beneficial values to customers’ ink rooms while offering higher transparency for purchasing & management teams
Hexachase Flexipack Sdn Bhd, a customer of Siegwerk in Malaysia, has been implementing MyInkroom with great success. Since then, they have been able to significantly decrease the manual workload. Thanks to the digital tools, there is no need for manual tracking of inventory levels, stock and consignments anymore. With the connection to the digital platform they can now rely on an automated visualization in real-time. The system also supports in calculating the ink consumption and forecasting demands for the future. By eliminating redundant tasks, their staff can now focus more on critical processes. As the result, the switch to Siegwerk’s MyInkroom improved the company’s productivity and efficiency proved by numerous KPIs according to Tan Lin Yaw, Production Executive at Hexachase Flexipack Sdn Bhd.
To learn more about the installation & implementation of MyInkroom in SEA, contact us at ramalingam.rajagurulingam(at)siegwerk.com or nattaporn.sarika(at)siegwerk.com. To learn more about MyInkroom, check out this video or contact us at ashish.yadav(at)siegwerk.com or myinkroom(at)siegwerk.com
Related insights: How automation can boost your ink room management