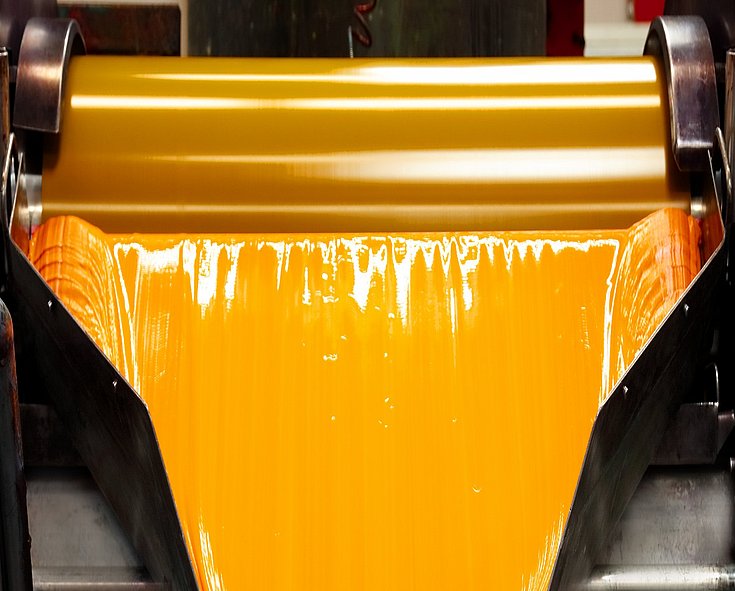
Colors are passion, emotions and personality. At Siegwerk, inks and coatings are our specialty and we use color to bring the packaging and products of our customers to life.
Product and consumer safety first
Siegwerk is a leading expert when it comes to safety for Nutrition, Pharma & Hygiene (NPH) packaging applications. We are committed to select high purity raw materials with least migration characteristic. In order to demonstrate this, we are transparent and provide in our Statements of Composition (SoC) information on all relevant migrants and support for safety evaluation. This gives our customer peace of mind for safe use of inks for printing, conversion and end-use of your packaging.
Depending on the individual formula of printing inks, solvents make up about 40 to 70 per cent of printing inks. Being a major component in flexible packaging inks, the impact of toluene is not to be taken lightly. Toluene has an unfavorable toxicological profile, prolonged exposure impacts on occupational safety (ototoxicity), besides being pollutant to the environment. Residual toluene on prints can easily affect the organoleptic quality of food (odor and taste).
Global trend towards toluene-free inks
Due to the negative aspects of toluene, many global brand owners have restricted or banned the usage of toluene in inks used for packaging material of their products. Another example of commitment to be toluene-free is initiative taken by Food Safety Alliance for Packaging (FSAP), a coalition of brand owners and other parties involved in the packaging chain.
Toluene is also restricted in many parts of the world, such as the European Union, Switzerland, and China. Most recently in India, the Bureau of Indian Standards (BIS) has officially imposed a ban on the use of toluene in food packaging inks.
Holistic transition approach
However, as toluene-based inks are cheaper and less awareness on its potential threats, printers still use inks with this solvent. Due to Siegwerk’s comprehensive technical and empirical know-how, the company supports printers with the transition to toluene-free packaging inks by applying a holistic approach. Our experts from the Process Management and Consulting (PMC) department are our specialized contact persons. They assist customers on site and help them manage their ink room. As the ink price is only the tip of the iceberg, the PMC team considers the customers’ “Total Cost of Ownership”, helping them to optimize their whole printing process – from pre-press and ink preparation to production. In the pre-press, our experts help optimize cylinders configuration. Concerning inkroom management, they support customers with the reduction of stock levels and ink waste, color matching times, and printing press downtimes. They guide to improve effective production time and print speed with toluene-free inks. After all, inks containing toluene need more time to dry and therefore limit the printing speed. These are only some examples of how our PMC team supports customers in optimizing their processes. In the end, printers can benefit from higher efficiency across the whole value chain absorbing extra costs for toluene-free packaging inks.
Successful transitions of SEA printers
In SEA, several printers have successfully managed the transition with our help. To name just a few examples: we solved one customer’s pain by simplifying the product portfolio from three ink series to just one high pigment ink system. For another one, we reduced coating weight by optimizing cylinders to achieve good and sharp printability. For a third one, we analyzed the existing color matching process in the inkroom and optimized color mixing formulation by reducing the percentage of violet inks, the most expensive ones. Finally, we helped different printers identify main causes for speed losses and improve press print speed.
Tailor-made transition solutions
Why is it worthwhile to manage the changeover to toluene-free packaging inks with Siegwerk? Very simple: our PMC team closely partners with our customers right from the start. At the beginning, we carry out a status analysis on site to evaluate all printing-related processes. This is the basis for a project plan tailored to our customer’s needs. Our On-site Consulting experts deliver an outside view and provide objective input which helps printers detect improvement potentials. This is important since our customers, as specialists in their field, are deeply involved in their day-to-day business and naturally lack this external perspective. During the entire transition process, printers benefit from continuous support, technical competence, and innovative problem-solving approaches. We build up a specific transition team adapted to the reality of the individual customer’s business and with proven experience across Asia. Our expert team in SEA consists of 5 consulting specialists. Contact persons are [ramalingam.rajagurulingam(at)siegwerk.com; Ramalingam Rajagurulingam Head of Process Management & Consulting Services, SEA-North, Hari.Noegroho(at)siegwerk.com; Hari Noegroho , Process Management & Consulting Services, SEA- South, ].
All in all, for SEA printers, banishing toluene-based packaging inks from printing processes with Siegwerk’s support is a gain in two respects: it demonstrates responsibility and sustainability while leading to a safer and more efficient performance.