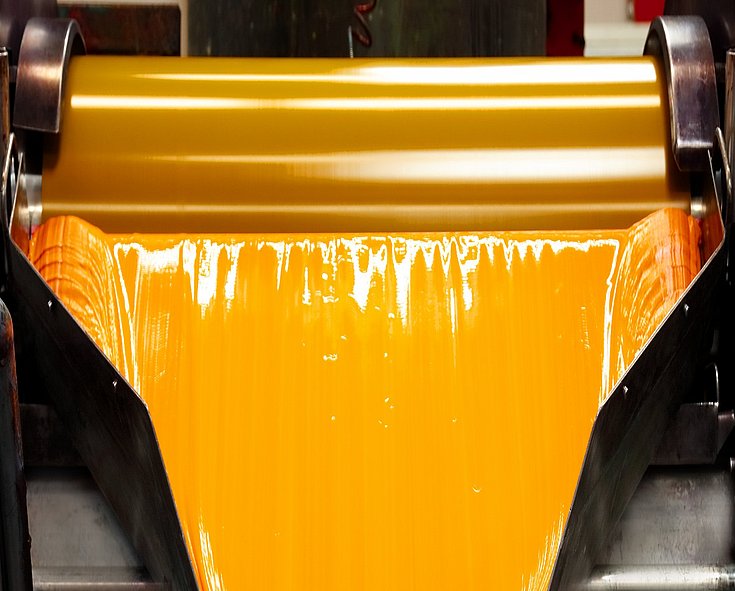
Colors are passion, emotions and personality. At Siegwerk, inks and coatings are our specialty and we use color to bring the packaging and products of our customers to life.
Q: In 2017 Siegwerk acquired SCHEKOLIN’s business unit “Plastic Tubes & Laminates”. How is this takeover related to Siegwerk’s current offering for PTL manufacturers?
A: Like all other acquisitions the main goal behind the purchase of SCHEKOLIN’s PTL business was to further strengthen our position as leading ink provider for packaging applications. By adding SCHEKOLIN’s UV varnishes suitable for plastic packaging including rigid tubes we specifically broadened our own portfolio of high-quality UV inks and varnishes especially for customers asking for specialty solutions for high-end packaging. Today, we offer a complete range of solutions including coatings, primers, varnishes and inks for almost every production and printing process.
Q: What exactly makes the PTL segment so interesting for Siegwerk? What’s the company’s concrete offering?
A: For tube manufacturers a smooth and fast production process is essential requiring high-performance inks and coatings. That means suppliers like us need a very high process expertise as well as profound know-how of potential interactions between coatings, primers and inks. This exactly makes the PTL segment a perfect fit for us. We are a well experienced partner of the industry with good connections to OEM machine manufacturers and a deep understanding of regulatory and brand owner requirements. We are a leader in product safety offering a broad range of migration optimized products and solutions meeting the individual needs of our customers for the intended end-use application. We always provide our customers with transparent and clear information about components, migration risks and recommended respectively excluded applications of each ink solution. With our ink expertise and high standards for safety and food compliance we support PTL customers to offer safe and efficient solutions standing out from low cost competitors. With the latest acquisition of AGFA’s UV inkjet ink business for labels and packaging, we now also offer ink systems for digitally printed tubes.
Q: What are key aspects of the “Plastic Tubes & Laminates” segment?
A: The market segment includes extruded plastic tubes as well as laminated tubes. Whereas extruded plastic tubes are mainly used in the pharmaceutical and cosmetic industry – primarily for high-end applications – laminated tubes are rather produced for mass market cosmetic products like for example toothpastes. Recently, PTL packaging is also getting used more frequently in the food industry. While laminates are mainly printed with flexographic presses, dry offset printing is the most commonly used printing technology for extruded tubes, even though the combination of flexo and screen printing for extruded tubes has already became a serious competitor for dry offset printing and respectively labeled tubes over the last 10 years.
Q: Do the PTL ink requirements differ from other packaging segments?
A: No, basically the PTL business has the same requirements than other packaging segments we currently serve. We have long-time experience in providing coatings and inks for all kind of packaging. Regarding ink formulation the PTL segment especially demands highly reactive ink series with good adhesion mainly on pre-treated Polyethylene and Polypropylene covering all kind of printing processes. Overprint varnishes for the PTL manufacturing have to particularly offer high chemical resistance to various kind of filling goods, high scuff resistance as well as good surface slip properties for processing the tubes in filling lines. Besides, tube manufacturers ask for optimal post-decoration properties as for example hot-foil stamping or screen printing which often gets applied on top of the tube coating.
Q: What are the market trends in this specific packaging segment?
A: In EMEA we for example see the trend to exclusively use low migration inks and coatings for plastic tubes. Besides, flexo printing is increasingly used for tubes today in order to especially achieve higher color brilliance and even better printing quality. Some printers additionally combine flexo with screen printing to achieve the same quality as when printing labels but instead printing directly on the tubes. For smaller production volumes many manufacturers of plastic tubes currently consider digital printing and shift to inkjet. Another continuous trend that we see is that brand owners are increasingly looking for optical or haptic effects such as soft-touch in order to differentiate their packaging from others on the shelf. Driven by brand owners and potential total cost of ownership savings, customers are generally more interested in eco-friendly and energy saving technologies like LED UV instead of conventional UV curing.
Q: What are your expectations for the development of the PTL business?
A: Considering the trend in EMEA towards the exclusive use of low migration products for plastic tubes, a further expansion of low migration solutions for all applications and printing processes will be demanded going forward. We already offer a specific migration optimized ink series for dry offset printing, for flexo printing we’re currently considering and testing existing product series for applications on plastic tubes. Even though there is still a very limited number of installed inkjet printing machines today, we will see further movement towards this technology in the PTL segment as it offers undeniable saving opportunities for small production volumes. Today, most of the major inkjet machine suppliers in PTL are already using the inks, that Siegwerk has recently acquired from AGFA. Due to the global number of installed machines dry offset printing will still have a bigger market share for the mass production of extruded plastic tubes. Furthermore, you can already note that aluminum tubes are more and more getting replaced by plastic respectively laminate tubes where possible for example for food or hair dye packaging. All in all, I would say that a small but steady and solid generic growth in the PTL market can be expected during the next years.