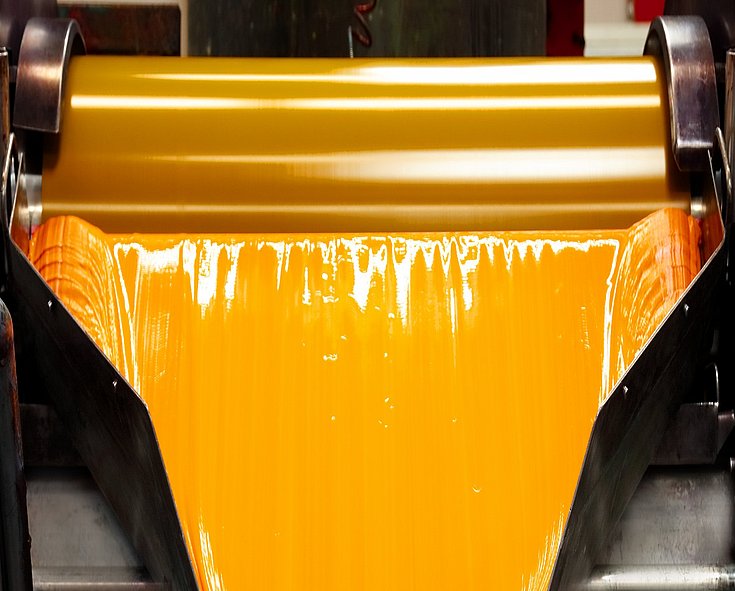
Colors are passion, emotions and personality. At Siegwerk, inks and coatings are our specialty and we use color to bring the packaging and products of our customers to life.
Siegwerk: Raja, what are typical challenges in almost every ink room?
Raja: Managing ink stock manually is a very time-consuming process that can easily lead to mistakes. It is not easy to always balance high and low consumed inks correctly. Thus, it is not uncommon that high consumption ink is running low while others become shelf warmers in the ink room. This usually results in the use of safety stock which in turn could lead to serious problems in case of emergency.
Siegwerk: How does a Vendor Managed Inventory System help here?
Raja: A digital Vendor Managed Inventory System basically enables the automation of ink room procedures. It not only helps to replace manual processes and thereby preventing manual mistakes, but additionally offers a precise real-time insight into stock levels and consumption rates. Based on data analytics it can e.g., also take over the automated reordering of ink and thus keep ink stock always at a defined level. With MyInkRoom we created a tool that makes it easier for our customers to exactly manage this balancing act between low inventory and high production planning flexibility.
Siegwerk: What are the features of MyInkRoom in this context?
Raja: MyInkRoom is a digital platform for automated ink room management that can be tailored to customers’ specific needs. It provides users with a fast, simple real-time overview of their entire inventories and dosing ranges as well as all other important KPIs at any time (24/7). It can be connected to ink dispensers but there is also a possibility to use it without a dispenser. The platform gives customers the opportunity to define product-specific reserve inventories themselves or have them automatically computed. If stocks fall below a minimum level, the system can prepare automated orders for replenishment in time. It is an easy-to-use tool and offers the opportunity to restrict access for individual users to selected features only. To unlock the full potential of the platform, our InHouse experts support each customer during implementation to best adapt the system to the individual requirements.
Siegwerk: So, why should customers use MyInkroom?
Raja: After implementing MyInkRoom there is just no need for manual counting or ordering anymore. Customers can easily monitor and control their stocks. Due to real-time consumption statistics, they become able to make accurate forecast ensuring the needed supplies are always available while outdated stock is continuously reduced. All in all, MyInkRoom can become an important time- and cost-saving tool for customers. The key benefits are greater transparency, increased cost effectiveness, fewer downtimes, and lower inventory requirements.
Siegwerk: Are there first success cases from practice?
Raja: As a continuation of our InHouse services we have implemented MyInkRoom for a few different customers so far. For our customer SPC Interprint, a manufacturer of converted paper products in Thailand, we for example transferred the inventory management from Excel sheets to MyInkRoom. Instead of manually tracking inventory levels, stock and consignments are now connected to the digital platform for a visualization in real-time. The ability to automatically predict inventory utilization for estimating future needs and the automatic ink order feature added significant value to the customer in terms of cost and expense savings and efficiency gains. Together with the customer we developed and implemented new routines, all accompanied by change management activities for ensuring a long-lasting success.
To learn more about installation & implementation of MyInkroom in SEA, contact us at ramalingam.rajagurulingam(at)siegwerk.com
To learn more about MyInkroom, check out this video or contact us at ashish.yadav(at)siegwerk.com or myinkroom(at)siegwerk.com
More details about how SPC Interprint and Siegwerk jointly reorganized the company’s ink room can be found here .