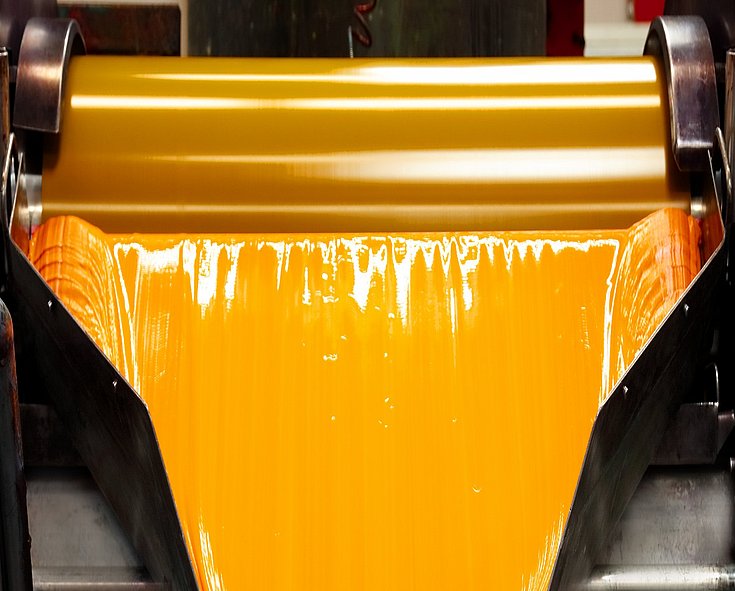
Colors are passion, emotions and personality. At Siegwerk, inks and coatings are our specialty and we use color to bring the packaging and products of our customers to life.
Q: What is the value of digital printing for label and package providers?
A: Today’s broader variety of print jobs, tight management of working capital and the make-on-demand philosophy are further reducing the average run length, making conventional print technologies less attractive. Here comes digital printing into play: It offers a solution to these challenges by maximizing print job flexibility and speed to market while minimizing machine setup-time and prepress costs. More and more label and packaging providers are already using digital printing for various markets today, whereby solutions for food and beverage packaging are of most interest. Above all, the inkjet technology is already fully adopted in the label printing industry and has high potential for the packaging market offering tremendous possibilities for growth.
Q: What is the biggest challenge for digital printed food packaging?
A: Producing food packaging or printing on food contact materials inevitably involves exposure to specific consumer safety concerns. Therefore, product safety is and will remain the most important and challenging aspect in food packaging independent of the printing technology used. Steady increasing regulatory efforts worldwide are continuously changing the general standards for ink formulations as consumer respectively packaging safety remains the highest priority. It is incredibly important that the packed food is not contaminated by the packaging for example through migration. Therefore, packaging printers and converters have to deal with a multitude of parameters when converting the various material streams including substrates, inks and adhesives into the ready-made printed packaging. All these parameters have a pivotal influence on the product safety and compliance status of the final food packaging making open exchange and transparency along the packaging value chain absolutely essential.
Q: How is Siegwerk supporting its customers in terms of product & food safety?
A: As a leading manufacturer of safe analog and digital inks, Siegwerk is well positioned to support customers in terms of e.g. regulatory guidance, exposure assessments, safety & toxicological evaluations and migration tests. At our innovation hub for digital printing solutions in Annemasse, France, R&D, production, and testing capacities are concretely dedicated to inkjet technology. Optimal testing opportunities at our Technical Center enable us to simulate and test printing results on almost all kind of flat substrates using different printing head technologies. Besides, we have a team exclusively dedicated to safety regarding both regulatory compliance and brand owner requirements to always ensure that our products are safe for the end-use applications. We permanently exchange with our customers and adapt our solutions to their needs without compromising on safety standards. It is all about transparency along the value chain. In this context, Siegwerk has a comprehensive raw material introduction process striving to achieve complete knowledge of the chemical composition of all raw materials intended for sensitive applications including food, pharma and hygiene packaging. Beyond that, we also carry out risk assessments and real case migration testing for customers. Besides, we have a strong network of partnering institutes and laboratories complementing our own analytical capacities and expert support. Siegwerk understands safe packaging and can also support in e.g. testing bond strength values, chemical resistance, or non-fade properties. With our Ink Safety Portal, we offer concrete insights into expert knowledge on consumer safety related topics like e.g. raw material qualification, compliance, risk assessments or migration testing.
Q: What is Siegwerk’s digital ink offering about?
A: Today, we offer a unique variety of high-quality inkjet ink solutions for all application areas in label and packaging printing including standard and sensitive applications as well as primers and OPVs suitable for various scopes. Our portfolio covers both UV inkjet solutions for a wide range of applications including self-adhesive labels, wet-glue labels for beverages, direct printing on 3D-packaging objects or blister and aluminum lids for pharma and food products as well as customized water-based inkjet ink solutions for tissue printing and digital printing on flexible packaging. From standard CMYK inks for labels, through specialty inks for coding applications or custom-made spot colors to migration optimized inks for sensitive food and pharma packaging, we always offer a suitable solution concretely adjusted to the final application and not only for a given printing equipment. For us customization goes beyond classical color matching, it also involves optimization of adhesion, mechanical and chemical resistance properties as well as assessment of migration risks.
More about Siegwerk’s digital printing offering can be found here.
For Product Safety & Regulatory related know-how check out Siegwerk’s Ink Safety Portal.